Silicon vs Silicone: Tariffs and Naturally Limited Resources
Silicon vs Silicone: Tariffs and Naturally Limited Resources
The Market
2018 was the most difficult year so far for end users of silicones. The price of silicone fluid (polydimethylsiloxane) rose from about US$1 per pound to US$3.60 per pound, and the price of silicone rubber (hydroxy terminated silicones) rose from US$1 per pound to US$2.80 per pound. The entire market was afraid they would not be able to secure enough material, so to guarantee uninterrupted production buyers purchased excessive allotments, exacerbating a shortage in an already strained market. This presented an excellent opening for the producers of silicones to increase price and profit margin. Manufacturers with the capability to turn silicon metal into silicones saw record returns of 200%-300% in 2018 for products that previously turned only a humble profit.
As lucrative as 2018 was for silicone producers, it was equally as catastrophic for their end users. Silicone end users were presented with an impossible choice: pass on an incredible increase in cost to their customers or sacrifice all their profit to retain market share. The silicone market in the US had never been such a nightmare. At the peak of the shortage in summer of 2018 and for reasons that remain unclear, silicones were included in list 2 of the 301-case brought against China by the Trump administration. Meaning, amidst a silicone shortage and record profits for the two major domestic manufacturers, the administration somehow saw fit to levy a 25% tariff on imported silicone from China.
Thankfully by October 2018 silicone production plants everywhere started the process of expanding their capacity to chase the tempting 200%-300% profits, and inadvertently alleviated some tension in the market. But as of May 2019, pricing still remains burdensome for many silicone end users and the 25% tariff on imported silicone from China still remains. Silicon metal (the feedstock for silicones) also carries an outdated anti-dumping assignment of 139.49%. This article breaks down how the silicone shortage could be alleviated or even prevented by applying free market global trade and recognizing the position of naturally occurring resources.
Silicon metal anti-dumping
The main raw material for producing silicone is silicon metal. For reference there are only two major manufacturers in the United States who produce silicone from silicon metal, there is another one in Europe, one in Japan, and ten in China. Why is there so much more production in China? The answer is very simple: China has the largest reserves of cost-efficient silicon metal production in the world.
Silicon metal comes from quartz (quartz is a rock of mostly SiO2, like sand). Quartz with commercial production value is mainly found in China, Brazil, Europe and the United States. In these locations the Si% is comparatively high, making quartz in these areas more cost efficient. In recent years the production of silicon metal in China yielded more than 2.2 million metric tons. The United States only produced 150,000 to 170,000 tons, and Europe produced between 420,000 and 460,000 tons. At the height of China’s silicon export history only 7,000 tons were sent to the US. The US market constituted <1% of China’s production.
Currently, most silicon metal produced in China is also consumed by China and its immediate neighbors, with little to no exports to the United States and Europe. This stems from the US anti-dumping case on Chinese metal initiated by five silicon metal producers in the United States in August of 1990. The result of this anti-dumping case was a tariff on Chinese silicon metal imports into the US of 139.49%. It might have felt like a win to US silicon metal producers, but the new tariff was a double-edged sword. Artificially high prices were realized immediately (table 1) when silicon metal increased by 50% from $0.42/lb to $0.61/lb. By 1996, another huge increase from $0.69/lb to $0.89/lb was so sharp in fact the DOJ alleged US producers were engaging in price fixing, causing the price to return to the previous year’s level in 1997.

Table 1: Silicone Metal Price 1989 – 1997 (US dealer import prices from “Metals Week” & “Platt’s Metal’s Week”)
Blocking imports from the largest silicon source in the world was not enough to save the five US silicon manufacturers who petitioned for the anti-dumping case, and unfortunately four of the petitioners completely shut down their silicon metal operations years after they won the case. With Chinese material rendered uncompetitive with the 134.49% tariff, US silicone manufacturers still needed silicon metal to produce silicone. The current domestic sources still must supplement their production with material from other countries (graph 1).
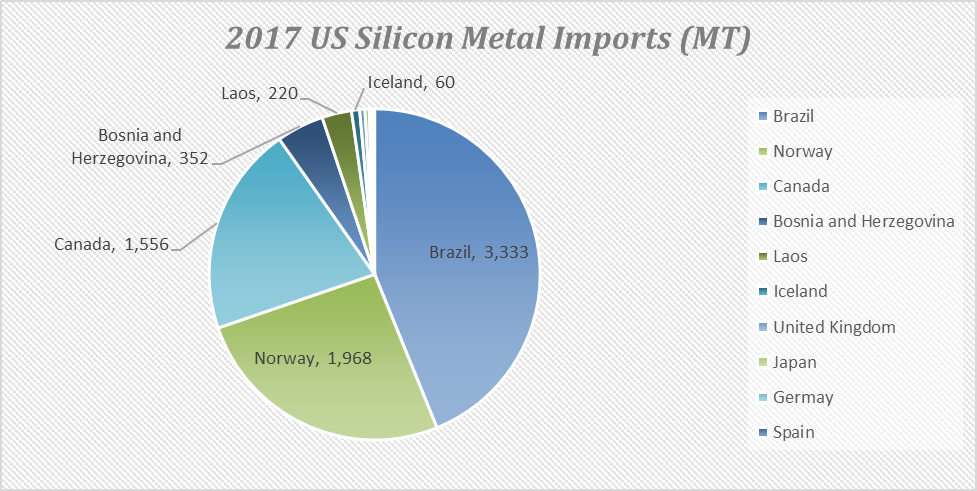
Graph 1: 2017 US Silicon Metal Imports (MT) (U.S. Census Bureau)
Losing low cost silicon metal sources for the US has driven up the price of silicones significantly. The downstream silicone market is far larger and more complex than the silicon metal market, with much higher-value finished products. On top of silicon metal price increases driven by anti-dumping, in late 2016 a major European silicone manufacturer shut down while a strike in the US closed another source for several concurrent months creating the global silicone shortage. All over the world, silicone manufacturers took this opportunity to massively increase their price. The manufacturers say that their margin on silicone either doubled or tripled in the past two years.
Once again, there are only two major manufacturers of silicone in the United States. One has their own silicon metal production (albeit not enough) and imports more silicon metal from Brazil. The other relies on outside silicon metal sources both domestic and imported.
Total imports of silicon metal from Brazil and other countries in 2017 totals over 7,000 tons. In fact, before the anti-dumping case was announced, China was exporting around 7,000 tons of silicon metal to the United States each year, which is less than one percent of China’s total production. However, this quantity played a decisive role in balancing the silicone price in the US and European markets. After the antidumping case went into effect in 1991, Chinese silicon metals companies were effectively rendered unable to export to the United States. This put immense pressure on Chinese silicon metal manufacturers to adapt their strategy. The result? Many small silicon metal plants closed or merged with large silicon metal companies, centralizing the once competitive industry. After integration the large silicon metal companies had greater capabilities and more capital. They quickly specialized in the development of downstream silicone products and specialty silicone fluids.
As a result, the anti-dumping against silicon metal lead to the opportunity for Chinese producers to begin manufacturing these downstream high-value silicone products and exporting them to the US and Europe, allowed them to capture even more market share than silicon metal ever held.
Silicone manufacturing and 25% tariff
On March 22, 2018, President Trump instructed the USTR to impose tariffs on $50 billion of Chinese imported product in order to punish China’s unethical practices surrounding US intellectual property. The administration stated that the tariffs would boost American manufacturing by increasing the cost of similar goods coming out of China. On June 15th of that year, the first list was published of $34 billion worth of items to receive a 25% tariff following a second list with the remaining $16 billion published on July 6th. Included on this second list was all Organo-Silicone products, during the most critical silicone shortage in recent history that had many USA manufacturers relying on Chinese silicone sources. The 25% tariff on silicones ended up going into effect August 23, 2018.
Today, the availability and production of silicone has been a bit improved, mainly because the expanding capacity is beginning to satisfy demand. Unfortunately, the price has not recovered proportionally. A 25% duty on Chinese silicone is still in effect and has kept the price for silicone artificially high in the US. This tariff is incredibly helpful for the two silicone manufacturers in the US, but the thousands of end users of silicone are still suffering under absurdly high prices.
So, what have we learned? It is very easy to initiate an antidumping case, but short-term benefits for a select few companies may have a much more detrimental impact to the US economy as a whole. In this case, a not well thought out antidumping claim on silicon metal laid the ground work for China to overtake a much more important industry in the United States: Silicone production. Due to their natural resources and antidumping position of silicone Now history is threatened to repeat itself through the implementation of a 25% tariff on silicones that would have manufacturers in China develop their own end products. Today it is more important than ever for US companies to diversify their silicone supply and work with Chinese manufacturers to maintain competitive pricing for their downstream products.
Authored by First Continental International (FCI). FCI is a supplier of silicones fluids, OH polymers, and specialty silicones with manufacturing in China. FCI can provide very competitive pricing and high-quality products to encourage and support downstream production in the United States and Canada.
Please contact FCI today for more information:
Michael Valenti, Vice President, 201-670-9868
Greg Heden, Senior Marketing Manager, 201-670-9887
Jeff Furbish, Marketing Manager, 201-670-9883
General Contact Information: 201 670-9848, Toll Free 1-888-999-1088, www.fci-nj.com